Challenges that industrial operators face when establishing common IP-based communications.
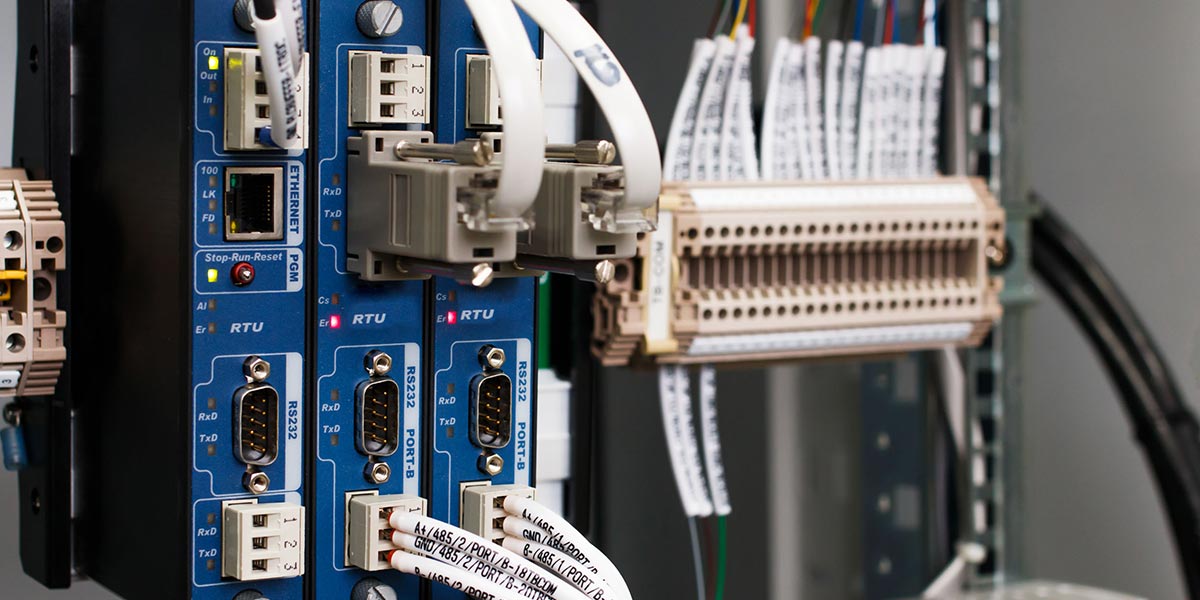
Many industrial devices now offer Ethernet connectivity built-in, but the overwhelming majority of communication and control still occurs over I/O, serial, and fieldbus connections. These legacy devices need to share data over a common IP-based communication platform in order to achieve greater automation and smarter operation. Here are the most common challenges that industrial operators face as they attempt to connect these devices to Ethernet networks.
Dealing With Multiple Standards and Protocols
There are quite a few industrial communication protocols and standards, each of which has a long history and an established base of users, equipment, and manufacturers. In many cases, it is out of the question for plant managers to replace installed and established equipment simply because it lacks an Ethernet port. Proprietary add-on modules may or may not be available, and it may be necessary to get creative or develop custom hardware. If multiple devices and interfaces are present in a single location, you may have no choice due to limited cabinet space.
Security Issues
With devices connected to a common network, any entry point to the network presents the possibility of unauthorized access if the proper measures are not taken. However, many industrial protocols were not designed with communications security in mind. These protocols were originally designed in an era where devices were expected to be physically connected to each other, and unauthorized use would be a matter of restricting physical access to those devices and facilities. As these devices connect to an Ethernet network, it opens them up to remote communication and control over that network. This is especially an issue because legacy protocols often do not support encryption or user authentication natively. Those devices are therefore wide open to access and control by anyone able to gain access to the network. This is a heavily-discussed concern for public utilities and other critical infrastructure.
High Bandwidth Usage
As industrial users try to leverage the advantage of having access to every aspect of their operation over the network, they are also encountering issues with bandwidth usage. Critical communications may be disrupted if a network is flooded with video or other traffic. If an operation has a lot of legacy devices that are all connected to the network, the network traffic to and from these devices also has the potential to overwhelm the network. This can be an issue with SCADA systems that are being used to obtain readings from hundreds of meters and sensors in the field. Finally, when all devices are connected into the same network, simple device alerts and automatic responses can quickly overwhelm the network in a broadcast storm.
Issues with Performance and Response Time
Ethernet communication is smarter and more scalable than serial-based communication, but there is inherent uncertainty about when individual Ethernet packets are received. Communication may be momentarily delayed if packets are dropped and resent. Serial communication, by contrast, involves direct physical connection and transmission, as well as fewer devices over shorter distances. If these differences are not properly accounted for, unanticipated issues can develop as devices request information over the network and do not get the immediate response they are expecting. For critical device communication, special accommodation must be made so that network traffic is protected and not delayed by other types of network traffic.
With thousands of industrial devices not equipped with any built-in Ethernet interface, connecting legacy devices to the network is a task that industrial users will continue to face for many years to come. Fortunately, solutions have emerged to address some of the main challenges. For example, the high bandwidth used by multiple devices being polled on the network can be mitigated with report-by-exception communication, local data processing, and/or industrial router. Communication between different industrial protocols can be handled by a standalone gateway or add-on module. Check out our various white papers for tips, such as
how to use EtherNet/IP to control a variable frequency drive that is designed for Modbus communication.
Have a question about this topic? We would love to hear from you. Please feel free to contact us and one of our representatives will reach out to you with more information.
Related Topics