Here's a list of real world industrial network deployment mistakes.
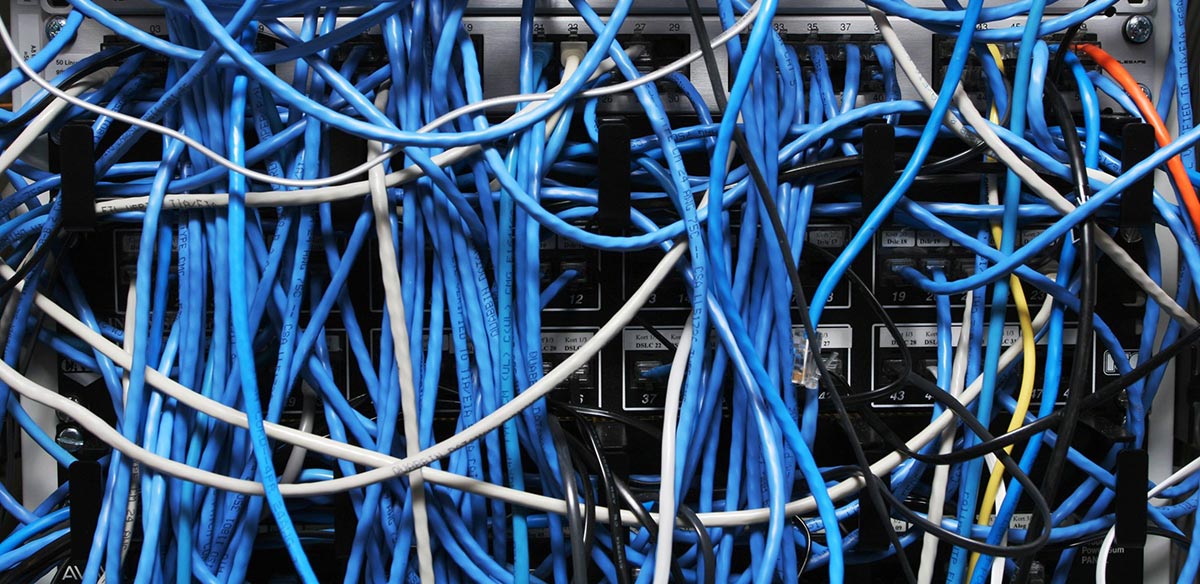
Over the years, our field application engineers have helped many industrial clients with their network deployments, and they have seen their share of hairy situations. We have collected some real-world mistakes that they have seen clients make below. Learn from their experiences and be sure to avoid these items if possible:
1. Not having a well-documented topology map of the network infrastructure.
When you do not have a good map of the network infrastructure, network issues become a lot more difficult to diagnose and manage. Which port is affected? What devices are connected to this switch? Where is it located? A detailed network map/diagram should have names, IP addresses, interconnection, wiring, protocols and location of major network devices.
2. Not having a defined and documented pattern or structure in assignment of network addresses and names
Whether you are troubleshooting a network issue or expanding the network, a haphazard approach to network address and names is very difficult to manage and much more likely to be entered incorrectly, especially as the network grows bigger. Ideally, you would like to have network addresses and names assigned in a structured and well-documented manner.
5. Not having
3. Poor cabling and wiring
Low quality cables and poor wiring practices is one of the most common causes of data transmission issues, and these can be among the most difficult to address after installation is complete. Cables should be tested and certified for the environments in which they are used in. One issue that comes up occasionally is Ethernet links between network closets and nodes that exceed the 100 meter specification – this can cause intermittent issues with data integrity. When cables are disorganized and unlabeled, that also makes it very difficult to troubleshoot physical connectivity issues.
4. Not updating hardware or firmware
Manufacturers occasionally issue updates to network hardware and firmware to address performance or security issues. In some cases, there may be critical vulnerabilities that were not recognized until after the product has been on the market for some time. Industrial users should not ignore manufacturer notifications and recommendations when it comes to updating their hardware or firmware.
5. Not having change management policies around patching and configuration of network devices
Change management policies help ensures that a network does not go down for unexpected reasons as it is expanded and new devices are added. If a planned network change causes an outage, the change management policies provides proper notification, coverage, and recovery. Without clear change management policies, network users may experience unplanned and unanticipated outages as administrators make unscheduled ad-hoc changes to the network.
6. Not establishing baselines to compare a healthy and not-so-healthy network
6. Not establishing baselines to compare a healthy and not-so-healthy network
If you know how your network traffic generally behaves under normal circumstances, abnormal traffic conditions and performance can be used as a flag to check for deeper issues. Ideally, the network performance should be documented over a period of time under normal conditions and a baseline created from which changes in performance can be measured. Without a baseline, it is much more difficult to determine if the network traffic is abnormal or not.
7. Network configuration has not been backed up or the backup file is out of date
For each network device, there are potentially many possible settings, addresses, subnet masks, filters, etc. to adjust for your specific network and topology. Having a network configuration backup saves a lot of time if a device needs to be replaced or reset back to a previous state. Not having an up to date configuration file available can greatly delay a network recovery effort as you try to remember or reengineer the specific configuration for your device(s).
8. Not restricting or managing access to network servers
8. Not restricting or managing access to network servers
It’s more than likely that your network servers provide the data communications backbone for your facility. For this reason, it is important to control physical access to the equipment and cabling. There should be a way to restrict who has physical access to the server room or equipment closet. Best practice would be to establish a log or tacking mechanism to track every time a person enters the server room, including name, time, and reason.
These are all common real-world mistakes that industrial users make when introducing or expanding their network. As you can see, most of these mistakes can be avoided with just a small amount of planning and effort. If you are establishing, expanding, or managing an industrial network, remember these common mistakes and try to avoid them as much as possible. This will help ensure a successful deployment and minimize the chance of network issues down the line.
Have a question about this topic? We would love to hear from you. Please feel free to contact us and one of our representatives will reach out to you with more information.
Related Topics
- Webinar: Building a SMART Network for the Industrial IoT
- Tips for Expanding Your Industrial Network
- 4 Common Issues With Legacy Devices and Ethernet Communication