Predict equipment failures before they happen.
Not to be confused with Preventive Maintenance, Predictive Maintenance (PdM) is achieved by analyzing your equipment’s condition statistics. The goal is to anticipate equipment failure by constantly monitoring your machines during normal operation and alerting system operators when there are indications that the equipment requires replacement or attention. This means you’ll need to take measurements on different dimensions of equipment performance and condition, collect that data, analyze it, and compare it to current conditions.
Predictive Maintenance Through Monitoring Equipment
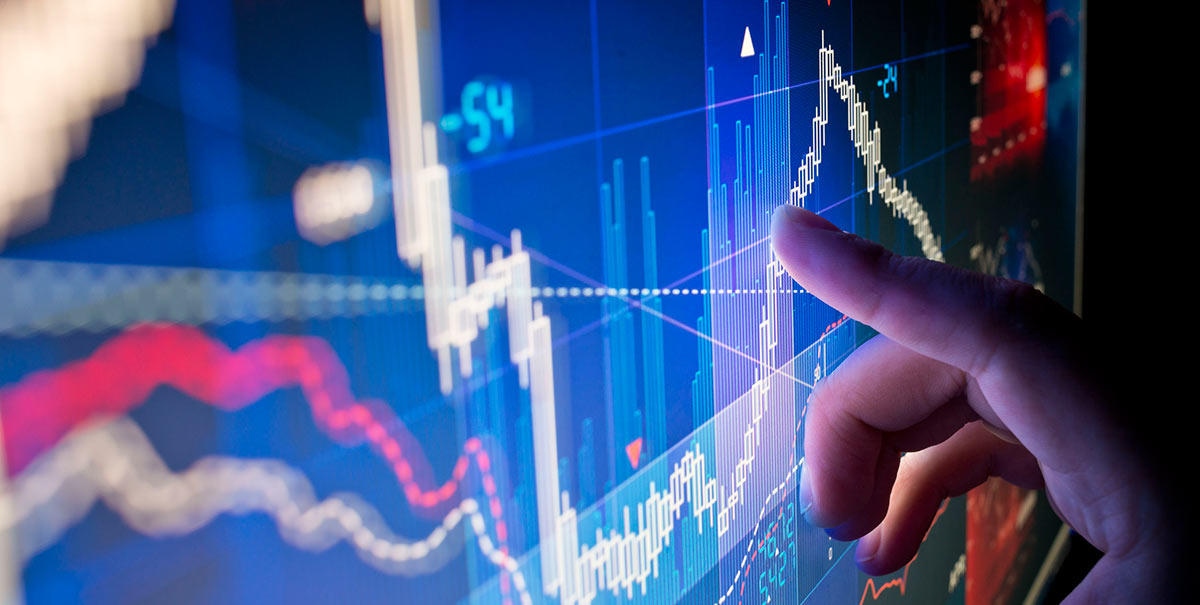
Here’s a simple example of implementing predictive maintenance to identify potential failures before they occur. A sensor is connected to a high-use wheel bearing, and live readings from that sensor are used to monitor its performance. An engineer is alerted if the sensor readings follow a certain pattern or falls below an established tolerance threshold. After being alerted, the engineer determines on site if immediate replacement of the wheel bearing is necessary to prevent damage to related equipment. This basic concept applies in multiple dimensions for mechanical systems to include other variables such as vibration, temperature, signals, and more.
With widespread adoption and development of networking technology to serve the industrial space, it is now possible and cost effective to monitor many more types of equipment in many different applications, ranging from CNC machines to solar panels and inverters. Cloud-based services have also emerged to making advanced analysis and dashboards much more accessible to the industrial user once the monitoring data has been collected. Establishing network connectivity and making data accessible to advanced algorithms is easier and more affordable than ever, making predictive maintenance easier to achieve for a wider range of devices.
Predictive Maintenance Through Monitoring Fiber Connections
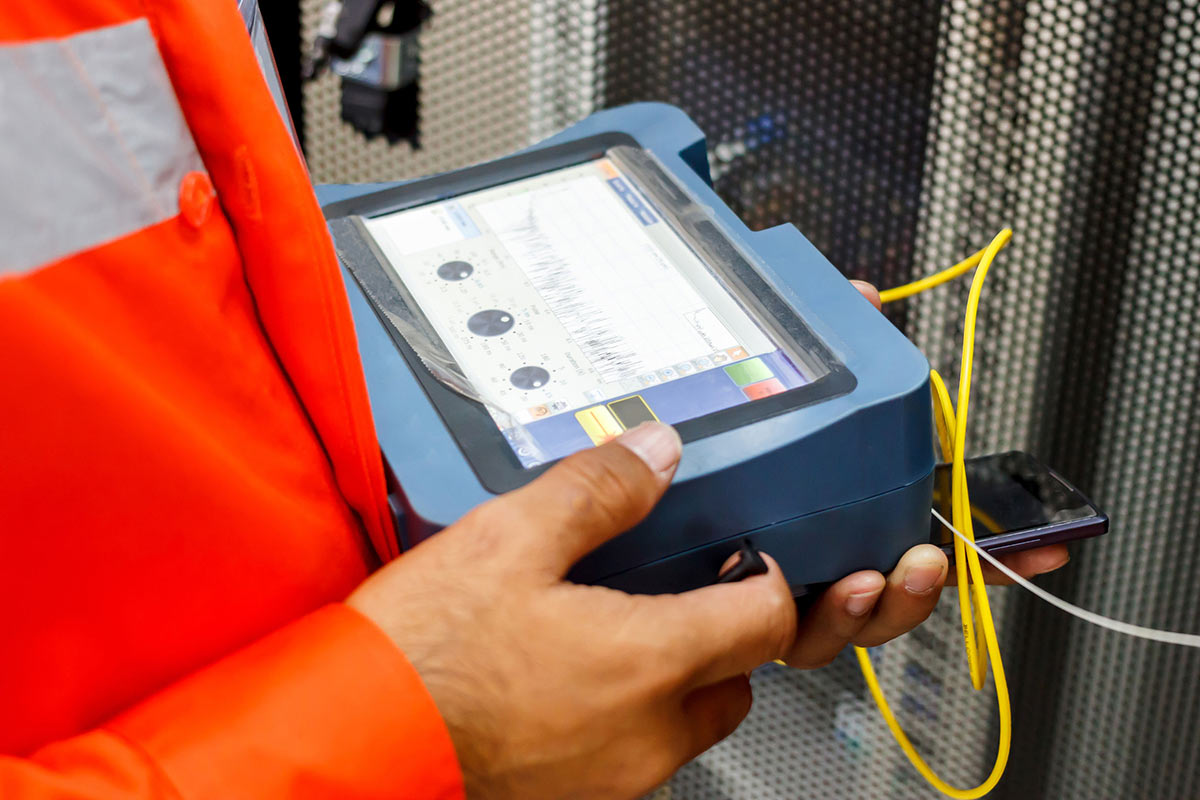
Predictive maintenance concepts can even be applied to the network itself. From a hardware standpoint, some fiber Ethernet switches now have built-in sensors that measure the strength of the fiber signal. Even when data is transmitted without error, if there is a notable change in the strength of the signal, that may be an indication that there a unit is in imminent need for repair or replacement. A technician can be alerted via SNMP trap or MMS to diagnose the unit and determine what action to take, before the network itself has been affected. This is exactly what predictive maintenance intends to do – make it possible to continue operations and minimize unscheduled downtime through pre-emptive action guided by data.
Leverage Technology to Help with Predictive Maintenance
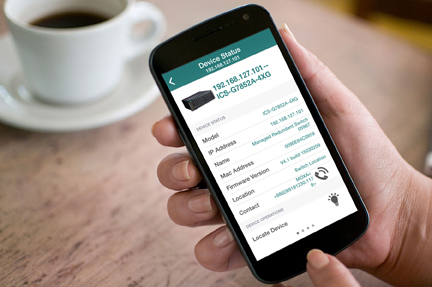
Predictive maintenance is not a new concept, but industrial users have a growing number of options to apply predictive maintenance to their operations and to their network to further minimize downtime. Mobile applications are now available that allow operators to monitor and manage their network while on the move. More information on mobile networking and its benefits can be found in our white paper: Enabling Mobility in Network Monitoring
Benefits of Predictive Maintenance
By monitoring machine and network performance, it is possible to actually prevent downtime from occurring by taking action before a device fails. There is another benefit to predictive maintenance - organizations are often better equipped to understand equipment performance and production quality and can tune their operations not just to minimize downtime, but to improve efficiency and yield.If you are interested in learning more about collecting machine data for predictive maintenance, let us know and we can have one of our representatives reach out to you with more information.