Prove the Value Through Potential Savings
When looking at all of the benefits that the Industrial IoT has to offer, you might be wondering:
“This all sounds great in theory, but it looks expensive. How will I be able to prove that this is a worthy investment?”
Identifying the value of the investment is a logical approach to every business decision. When asked to show this for IIoT technology, you must first understand that the impact of IIoT affects many aspects of a business. There are many components that enable IIoT, from the networking equipment that extracts data from industrial devices, to the software and applications that project meaningful information for the end user.
To complete the evaluation, you’ll need to include expenses, as well as any cost reductions from implementing the new technology. For example, IIoT benefits include operational efficiency, reduced downtime, fewer maintenance calls, and more – all of which are tied to a dollar amount. Making sure that every costs and potential savings is outlined will help you get a more accurate payback period estimate for your new investments.
IIoT implementations generate many advantages for a business. Some of these are often overlooked, but actually result in big cost savings. Let’s take a look at some examples where the IIoT can help reduce costs.
Identifying the value of the investment is a logical approach to every business decision. When asked to show this for IIoT technology, you must first understand that the impact of IIoT affects many aspects of a business. There are many components that enable IIoT, from the networking equipment that extracts data from industrial devices, to the software and applications that project meaningful information for the end user.
To complete the evaluation, you’ll need to include expenses, as well as any cost reductions from implementing the new technology. For example, IIoT benefits include operational efficiency, reduced downtime, fewer maintenance calls, and more – all of which are tied to a dollar amount. Making sure that every costs and potential savings is outlined will help you get a more accurate payback period estimate for your new investments.
IIoT implementations generate many advantages for a business. Some of these are often overlooked, but actually result in big cost savings. Let’s take a look at some examples where the IIoT can help reduce costs.
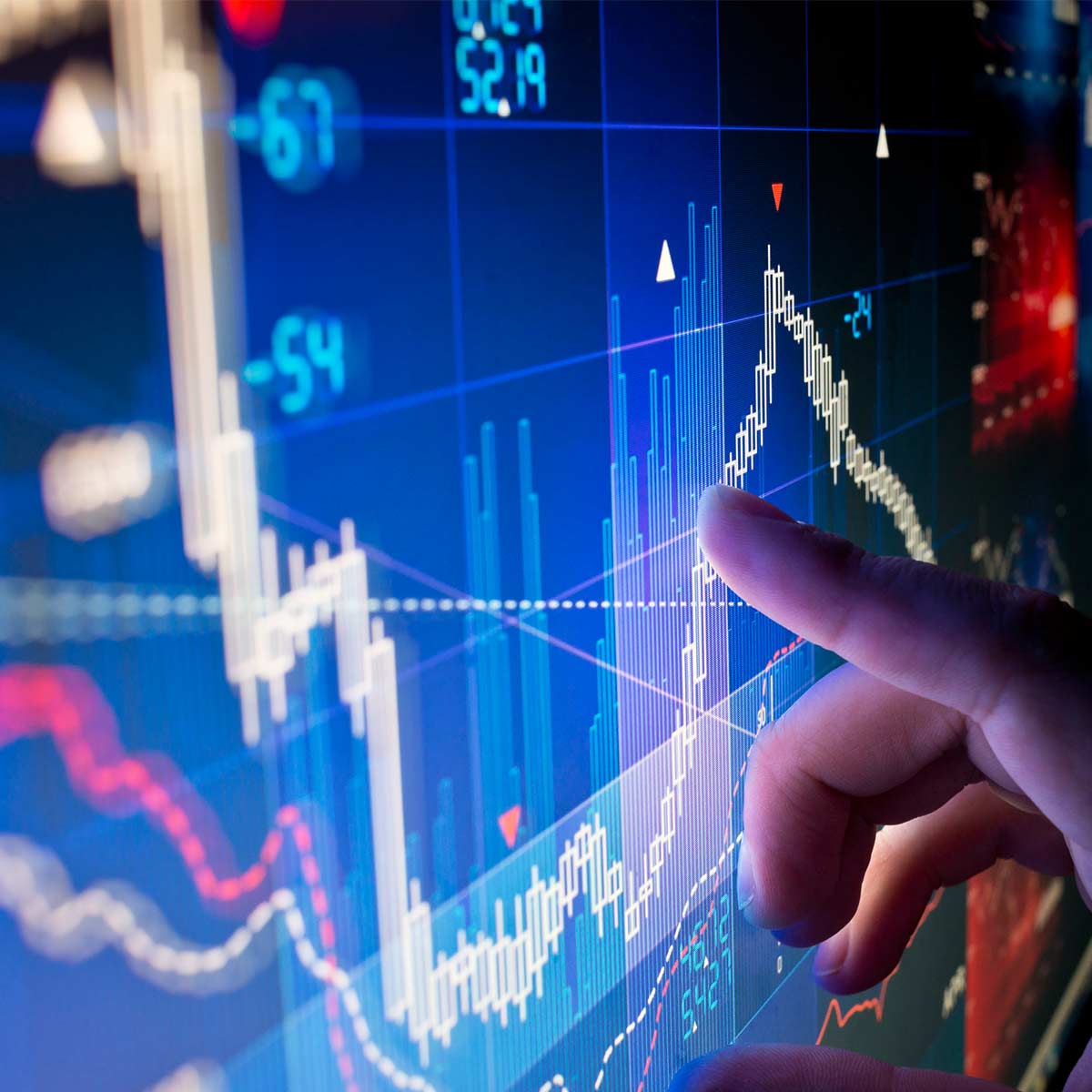
Parts and Labor
One of the most sought-after benefits of adopting IIoT is Predictive Maintenance. With the wealth of data you can extract from IIoT connected equipment and sensors, operation managers can apply Predictive Maintenance techniques to execute proactive services and repair to equipment that is performing at sub-optimal levels.
With performance data provided in real-time, organizations can address problematic components prior to failure, extend the lifetime of expensive capital equipment, and greatly reduce system downtime. Depending on the application, even minutes of downtime avoided already means astronomical amounts of money saved. On top of this, let’s not forget the cost of replacement components.
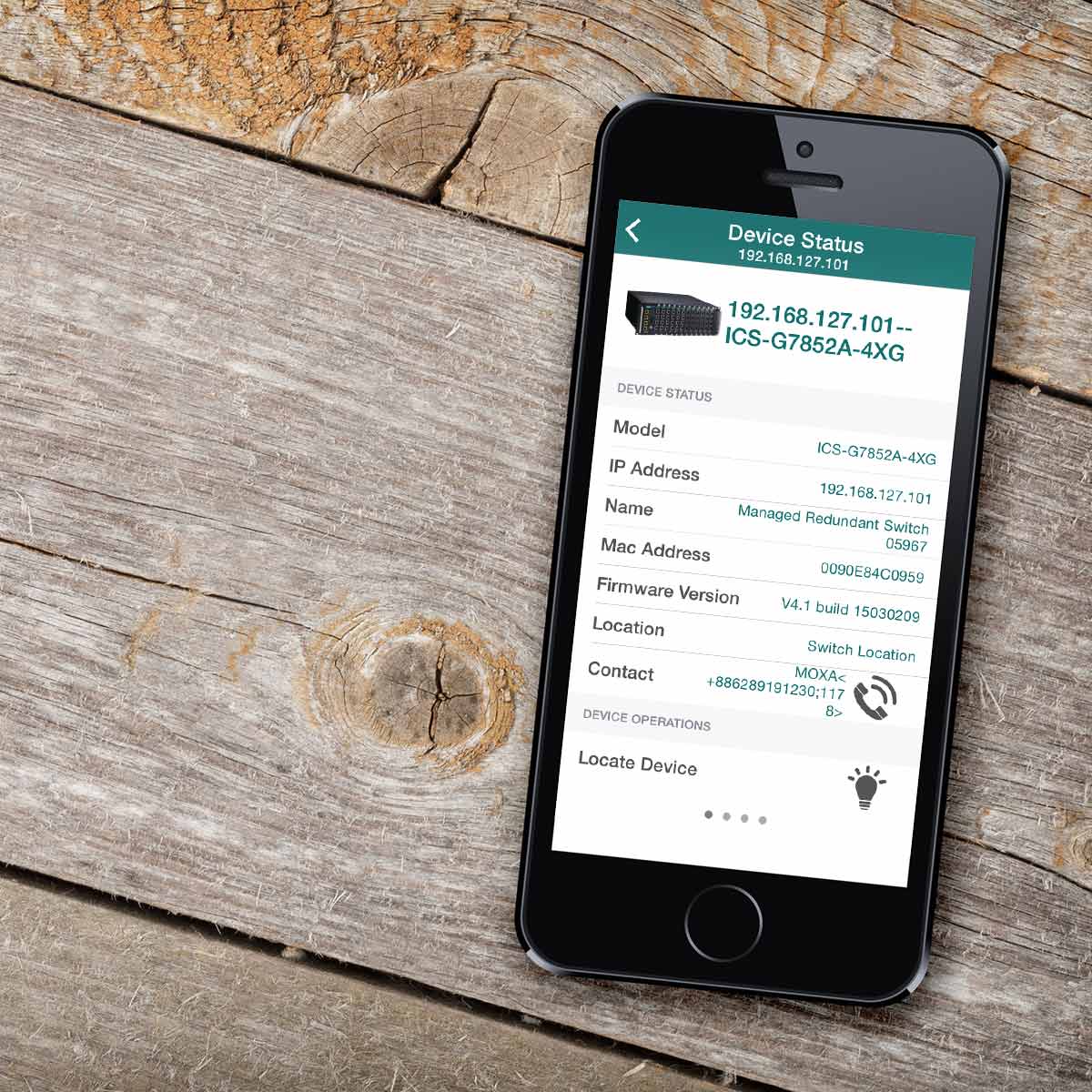
Remote Monitoring
As many are aware, remote monitoring is another great benefit of enabling IIoT. With remote monitoring, system health can be evaluated when maintenance technicians need to be mobile or while traveling outside the country. This allows greater flexibility and also makes global operations easier to conduct. As system notifications are sent to technicians, they can evaluate the issue and determine whether immediate maintenance is required. With this efficiency, the number of maintenance visits can be reduced, which also means a reduction in travel costs.
When the “Things” of your application are connected to the internet, not only can you monitor the entire system, but can also have the ability to drill down to specific device performance. As a result, maintenance becomes a lot more efficient, as problematic areas can be pinpointed for repair. This saves significant amounts of time and effort as opposed to having engineers check the entire system for the source of the issue. Like they say, “time is money”.
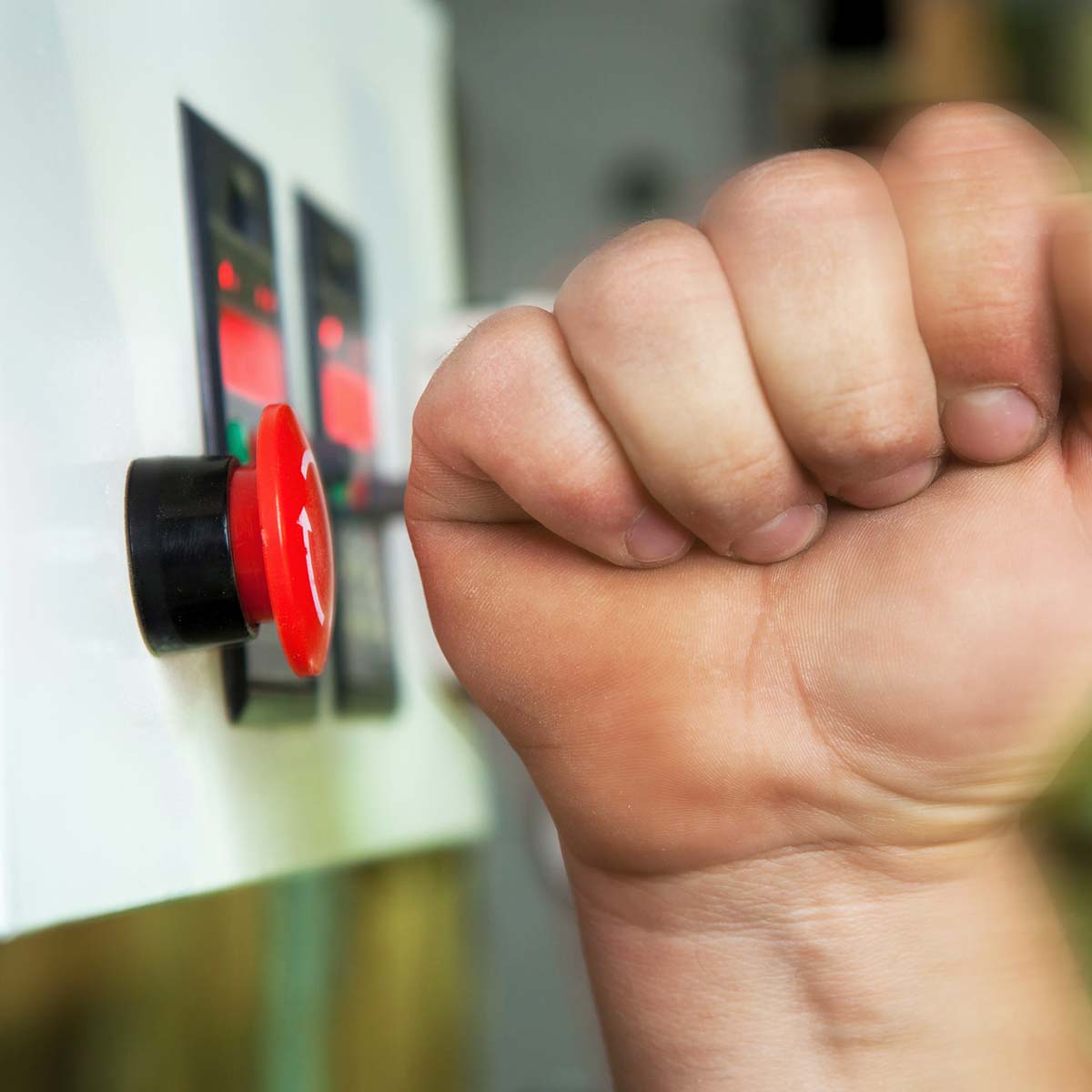
Material Waste
When manufacturing facilities experience a disruption in their automated processes, this can mean anything from poor product quality to complete system downtime. Both of these scenarios have cost associated with them that should be considered for potential savings. Most of us understand the cost of downtime and how this can be calculated. What about poor product quality? Businesses with strict quality control policies usually won’t sell products with sub-par features. This results in material waste, as well as an amount associated with the opportunity cost of a salable product. In some cases, this may can also mean a production backlog and additional costs for making up missed schedules.
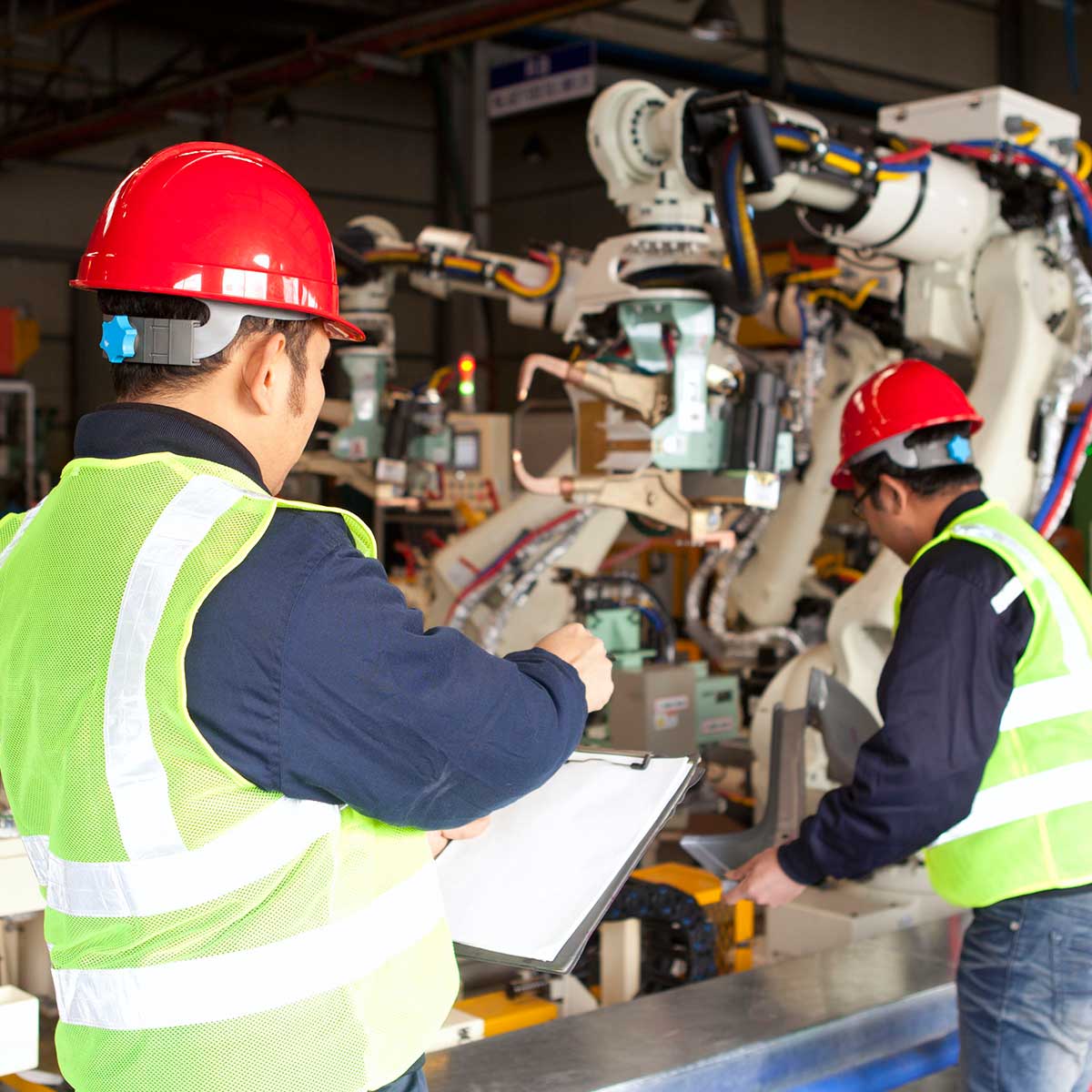
Process Efficiency
Regardless of application size, conducting an audit of the processes that take place in the current setup is a good start on uncovering areas for cost cutting. Working with operators and uncovering manual processes is a great way to identify areas to install sensors and monitoring for remote management. For example, if workers on a plant floor manually pull equipment performance data, this can be eliminated with sensors and by connecting devices to read those sensors. Doing so opens up employee bandwidth for other, less tedious tasks.
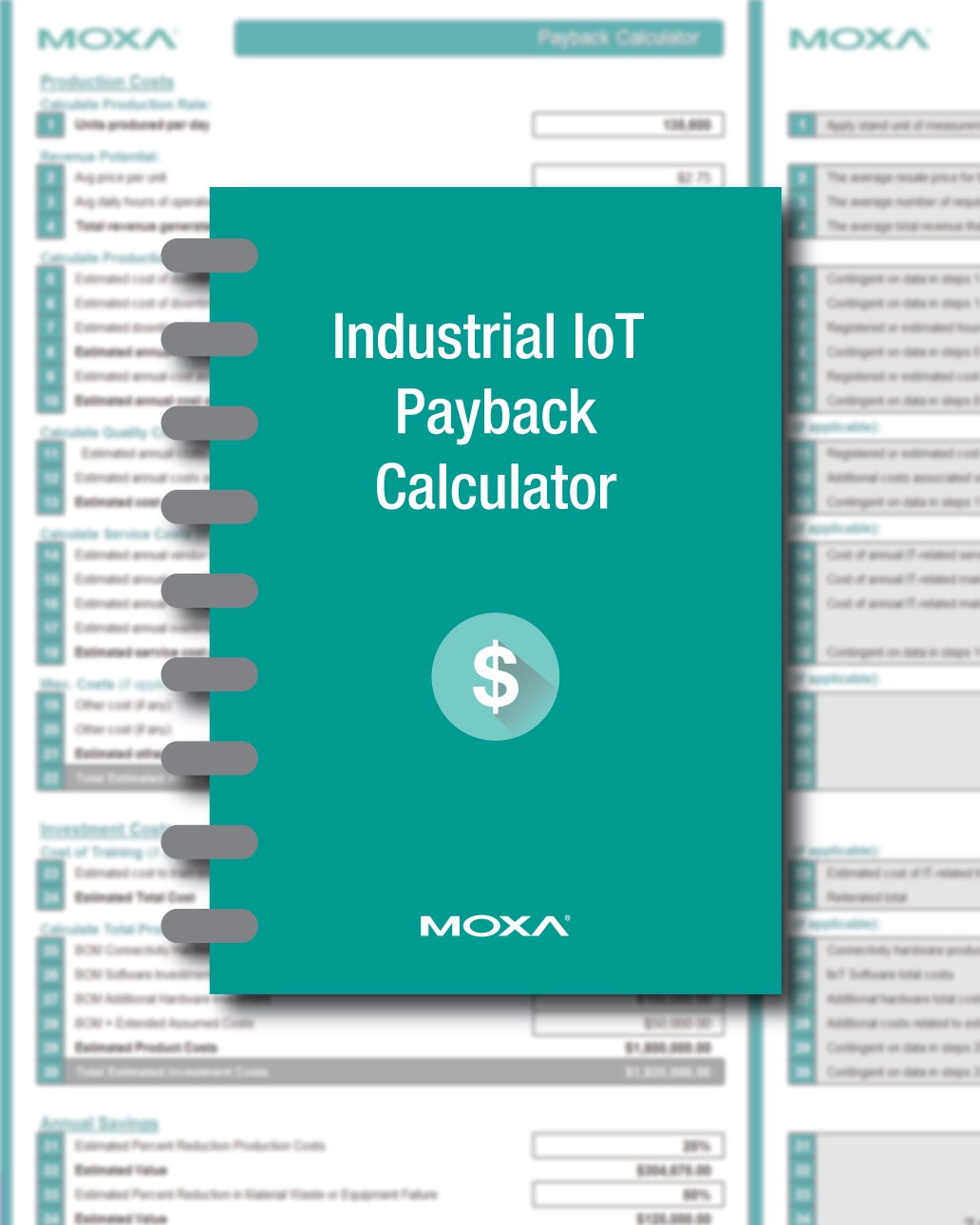
Estimate Your Payback Period
As mentioned, there are several areas where a business can benefit in cost savings with IIoT technology. They should all be considered as much as possible when evaluating your IIoT expenditures.
To help think through your cost considerations we’ve put together a Payback Calculator that compares your investment against some common areas of potential savings. The calculator has sections to enter your downtime costs, operational costs, and investment costs. The more costs and savings you can think of adding to this calculator, the closer the payback estimate will be for your IIoT investments.
*Due to every business and industry being unique, the payback calculator does not factor in every possible scenario for potential cost savings. This tool is solely intended to be a guide to help you get started with your estimate.
If you are interested in learning more about the Industrial Internet of Things, let us know and we can have one of our representatives reach out to you with more information.
Want more info like this?
Subscribe to learn more about the IIoT and Industrial Networking.